Comprehensive Guide: What is Porosity in Welding and Just How to Prevent It
Comprehensive Guide: What is Porosity in Welding and Just How to Prevent It
Blog Article
Porosity in Welding: Identifying Common Issues and Implementing Finest Practices for Prevention
Porosity in welding is a pervasive problem that usually goes undetected till it causes significant troubles with the honesty of welds. This typical problem can compromise the toughness and durability of bonded structures, posturing safety and security dangers and resulting in costly rework. By recognizing the origin causes of porosity and applying efficient prevention strategies, welders can dramatically boost the top quality and integrity of their welds. In this conversation, we will discover the essential factors adding to porosity formation, analyze its harmful effects on weld efficiency, and talk about the very best techniques that can be embraced to decrease porosity incident in welding procedures.
Typical Sources Of Porosity
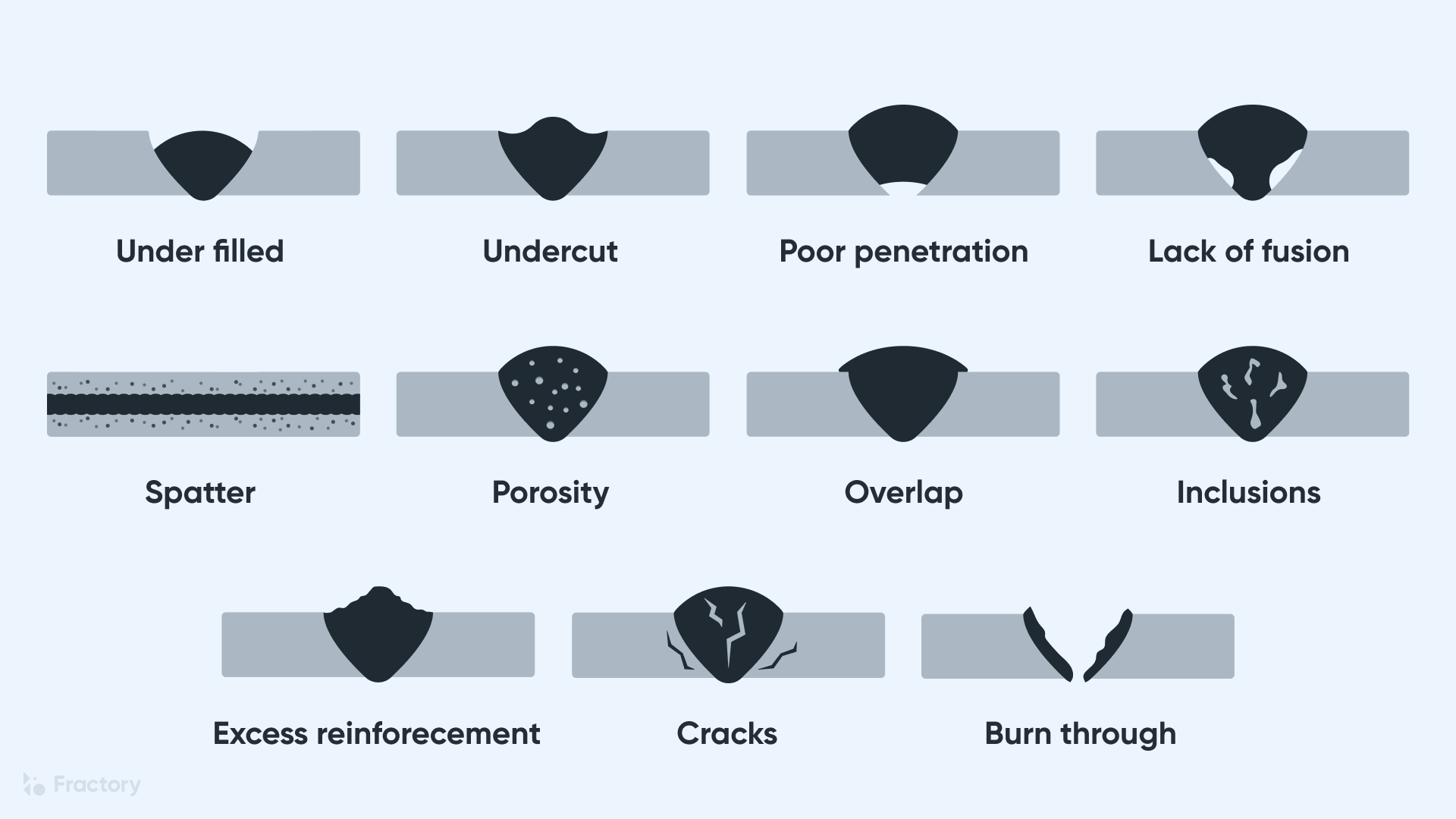
An additional frequent perpetrator behind porosity is the presence of pollutants on the surface of the base steel, such as oil, grease, or rust. When these pollutants are not successfully gotten rid of prior to welding, they can vaporize and become caught in the weld, creating defects. Furthermore, using filthy or wet filler materials can introduce impurities right into the weld, adding to porosity issues. To mitigate these usual reasons of porosity, comprehensive cleaning of base metals, correct securing gas choice, and adherence to ideal welding criteria are important practices in achieving high-quality, porosity-free welds.
Influence of Porosity on Weld High Quality

The existence of porosity in welding can significantly compromise the architectural honesty and mechanical residential or commercial properties of bonded joints. Porosity develops voids within the weld metal, damaging its general stamina and load-bearing ability.
One of the primary repercussions of porosity is a decline in the weld's ductility and sturdiness. Welds with high porosity levels tend to display reduced impact strength and minimized capacity to deform plastically prior to fracturing. This can be specifically concerning in applications where the bonded elements are subjected to vibrant or cyclic loading conditions. Porosity can hamper the weld's capacity to efficiently transmit forces, leading to premature weld failure and prospective security dangers in important frameworks. What is Porosity.
Finest Practices for Porosity Prevention
To improve the structural integrity and quality of bonded joints, what certain steps can be carried out to reduce the occurrence of porosity throughout the welding process? Porosity avoidance in welding is critical to make sure the stability and strength of the last weld. One effective practice is correct cleansing of the base steel, getting rid of any contaminants such as rust, oil, paint, or dampness that could lead to gas entrapment. Ensuring that the welding tools is in excellent condition, with tidy consumables and suitable gas flow rates, can also significantly reduce porosity. Additionally, keeping a secure arc and regulating the welding parameters, such as voltage, existing, and travel rate, assists create a consistent weld pool that lessens the threat of gas entrapment. Making use of the appropriate welding strategy for the certain material being bonded, such as adjusting the welding angle and weapon placement, can even more protect against porosity. Routine inspection of welds and instant removal of any problems determined during the welding procedure are crucial methods to stop porosity and produce premium welds.
Significance of Appropriate Welding Methods
Executing appropriate welding methods is critical in making sure the structural stability and high quality of welded joints, building on the structure of efficient porosity prevention steps. Welding strategies straight influence the overall stamina and longevity of the bonded structure. One vital facet of correct welding methods is preserving the appropriate heat input. Too much warmth can cause increased porosity as a result of the entrapment of gases in the weld swimming pool. On the other hand, inadequate heat may cause insufficient fusion, creating possible powerlessness in the joint. Additionally, making use of the ideal welding specifications, such as voltage, current, and take a trip speed, is essential for attaining audio welds with minimal porosity.
Additionally, the selection of welding procedure, whether it be MIG, TIG, or stick welding, must line up with the certain demands of the project to ensure ideal outcomes. Correct cleaning and preparation of the base steel, as well as picking the best filler product, are additionally crucial elements of proficient welding methods. By sticking to these best methods, welders can decrease the danger of porosity formation and her latest blog produce top quality, structurally audio welds.

Testing and Top Quality Control Measures
Quality control procedures play an important duty in validating the integrity and dependability of welded joints. Checking treatments are vital to find and prevent porosity in welding, guaranteeing the stamina and longevity of the final product. Non-destructive testing methods such as ultrasonic testing, radiographic screening, and visual examination are frequently utilized to determine potential flaws like porosity. These techniques allow for the evaluation of weld high quality without jeopardizing the stability of the joint. What is Porosity.
Post-weld assessments, on the various other hand, evaluate the last weld for any flaws, consisting of porosity, and confirm that it satisfies specified standards. Implementing a thorough top quality control plan that includes thorough testing procedures and inspections is vital to minimizing porosity issues and guaranteeing the total top quality of welded joints.
Final Thought
In verdict, porosity in welding can be a common issue that affects the quality of welds. By recognizing the typical root causes of porosity and applying best practices for prevention, useful reference such as appropriate welding strategies and screening measures, welders can ensure high quality and trustworthy welds. It is important to prioritize prevention approaches to lessen the event of porosity and preserve the honesty of page bonded frameworks.
Report this page